Have you ever wondered about the difference between quarter, rift and plain sawn floors? Well, here’s a primer for your reference. The way a log is cut by the saw will determine the orientation of the grain in the wood. This post discusses the difference between 1.) plain sawn floors – the default way of sawing in the modern world and 2.) quarter and rift sawing.
Plain Sawn Floors
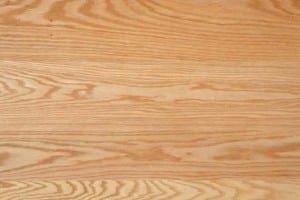
The most obvious difference between plain sawn and quarter and rift sawn flooring is appearance. Most flooring today is plain sawn. In plain sawing, character markings and figure patterns resulting from the annual rings are brought out more fully, including the characteristic cathedral graining that is so prominent in woods like Oak (see figure 1). Plain sawn floors also tend to be available in wider widths than quarter and rift sawn floors.
The face appearance of a floor plank is determined by the way the wood grain is exposed by the saw. All logs consist of concentric annual growth rings of wood, beginning in the center and moving outwards. In plain sawing, a log is moved back and forth on a saw carriage and rotated with each successive slice until it is cut from the outside inwards. With plain sawn lumber, the growth rings, visible at the butt end sof the boards, will typically range from parallel with the surface of the board to a 30 degree angle or more from the surface of the board.
Quarter and Rift Sawn Floors
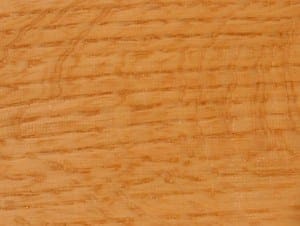
Quarter sawn floors are a relative rarity today and as such they have cachet among homeowners looking for the unique.
Quarter sawing slices perpendicular to the wood’s annual growth rings, resulting in a straight grain appearance that also exposes the medullary rays, producing a unique figure or fleck that is highly sought after for furniture and cabinet making (see figure 2). Those familiar with the Arts and Craft and “Mission Oak” style of the early twentieth century will recognize this fleck.
In quarter sawing, the log is first quartered and then the quarters are cut again into slices. This method produces both quarter sawn and rift sawn boards. The center boards (true quartersawn) will have growth rings positioned at 60-90 degrees to the board’s surface. This is best viewed from the butt ends of the boards. As the cuts are made from the quarters, they become more rift sawn (growth rings at 30-60 degrees from the surface). When flooring companies refer to quarter sawn wood, they are usually referring to a specialty wood flooring cut that is a combination of quarter and rift sawn.
The straight grain of quarter and rift sawn wood is very consistent, making it desirable among furniture makers. Because quarter sawn lumber takes more time to produce and produces less yield (there is no boxed heart left over to market as pallet lumber), it costs more than plain sawn. There is also demand for quarter sawn lumber among furniture and cabinet makers, boat builders, instrument makers, and others.
In Figures 3 and 4 we have room photos to more clearly illustrate how the appearance differs in plainsawn and quarter/rift sawn wood floors. Note how the grain in the floor shown in Figure 3, below, appears quite straight, with some waves of fleck.
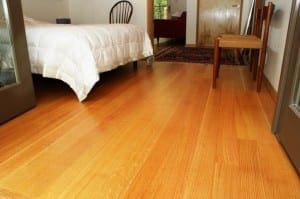
The overall look of a quarter and rift sawn Oak floor is entirely different from that of a plainsawn Oak floor, which has the typical cathedral or flame-shaped peaks that are very prominent and broad in the grain.
In Figure 4 we have an example of plainsawn Red Oak in a room setting. Here you can really see the beautiful flame-like peaks in the broad grain, which is what most of us think of when we consider Oak. Both floors are made from the same species and grade of wood. The only difference is in the angle of the saw cut and the color of the stain and/or finish chosen for the floors.
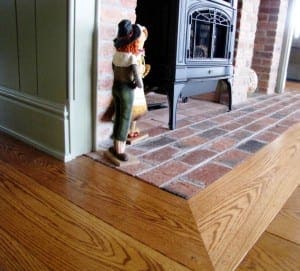
If you need to see the differences up close and would like to order samples of our flooring, we are happy to assist. Call 1-800-928-9602 or email us today.