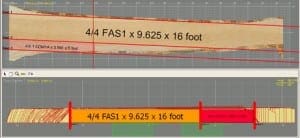
January 2004-Hull Forest Products Installs First-of-Its-Kind Edger
In 2004, Hull Forest Products installed and began running a new computer-optimized edger system that was the first of its kind in North America.
An edger is a machine that saws the round edges off boards from the saw carriage. This may sound like a simple task, but with thousands of boards sawn each day, even the best trained human operators can only be expected to perform at about 75 to 80 percent of optimal. Small errors in edging of 1/16 or 1/8 inch per board add up to significant lost profits.
With our new system, we have the ability to consistently saw products to within a couple of thousandths of an inch, yielding 97 to 99 percent of the optimal value recovery from each board. We can also saw fixed width, random width, and specialty products, as well as edge different thicknesses to different parameters, all in the same production run. This system has enabled HFP to provide more customized and value-added products to its customers, which benefits not only manufacturers and end users, but also landowners, who may receive more money for a given quantity of timber due to the increased value of a product that is manufactured using computer optimization.
The new edger cost over $1 million and is essentially a production rip saw that incorporates the latest in laser scanning and computer processing technology. In contrast with the traditional method of manually operating an edger (which requires extensive grading and math skills utilized in just a short moment to make the best decision on how to edge each individual board, at thousands of pieces each day), the new edger can process a day’s production and achieve the highest value solution on every board from the first to the last.
With minimal human input to identify grade zones and defects on the lumber, the edger scanners collect a high density 3D profile of each board within one foot of travel. As the board continues toward the saw box, the computer models the 3D data collected by the scanner and analyzes the geometric limitations of the NHLA grade rules across several grades, combined with relative values, to obtain the optimum solution based on human-entered variables combining appearance, grade, and recovery. The optimizer can evaluate over 20,000 independent solutions for each board in only tenths of a second. As the board approaches the saws, the computer finalizes its decision and directs the hydraulic system to position the saws at the correct angle and spacing. As the saws enter the cut, they slew at a rate defined by the angle and speed of the board. As the board exits the machine, it is pushed out onto the lumber deck, while the edgings are dropped into the by-product system.
The edger machine hardware was produced by Timber Machine Technologies (TMT) of Tualatin, Oregon. The scanning and software package was produced by Inovec of Eugene, Oregon. Inovec is a division of GE Infrastructure. The two companies have a history of working well together on sawmill optimization projects.
Our new edger installation was featured in The Timberline Magazine.